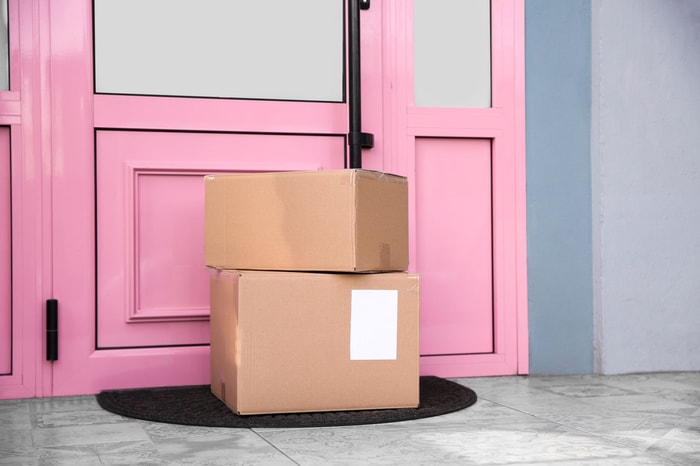
How to Pick, Pack, and Ship Orders Efficiently
Want to learn how the picking, packing and shipping system works? Here's what retailers need to know.
By Francesca Nicasio — 30 September, 2021
Customers today expect a lot from retailers. They demand utmost flexibility and want their orders to be shipped to them as quickly as possible.
Research shows that 84% of online shoppers are unlikely to buy again from a retailer after a single negative experience with their delivery. So, ecommerce stores must streamline their order fulfillment process in order to meet the demands of their customers.
Pick-pack-ship is an order fulfillment method used by many retailers to make faster deliveries and streamline the shipping process.
In this article, we'll delve into how the pick, pack, and ship system works, and how ecommerce businesses can go about streamlining their packing, quality control, and shipping processes.
What is a pick-pack-ship?
Pick, pack, and ship is the process of choosing the right items for a customer's order, packaging them appropriately, and then shipping them off to the customer. The process seems pretty straightforward, but there's a lot that goes on in the background.
The system only works if there is a purpose-designed order fulfillment center run by store managers that have a full grasp of order fulfillment and logistics management.
The process must ensure that accurate pick lists get to pickers, the right packing materials are readily available to packers, and that standard shipping boxes are ready for use when needed.
Benefits of an efficient pick-pack-ship process for ecommerce businesses
The pick, pack, and ship method will demand more work and accountability from your employees, but its transformative impact will eliminate errors, reduce the need for clearance sales, and boost store revenues. Here are some more of its benefits for ecommerce businesses:
- Speed and efficiency: A streamlined order fulfillment process ensures that products get to customers sooner while reducing errors and boosting efficiency.
- Happy customers: Customers are happy when orders are fulfilled accurately and on time.
- Cost-effectiveness: The pick-pack-ship method is designed to get orders to customers as efficiently as possible, and this reduces manual labor, which saves you money.
How does the pick-pack-ship process work?
You will need careful planning and adequate investment in staff training to make the pick-pack-ship process work, regardless of the size of your business. The workflow typically involves following steps:
- A customer order is sent to the fulfillment warehouse.
- A packing slip listing the items on the order is generated.
- The items are picked by a warehouse worker using barcodes on the packing slip to identify the right products.
- The items are taken to a packing station where they are boxed, sealed, and labeled.
- The package is then taken to the loading station from where carriers like FedEx or USPS will deliver them to the buyer.
Step 1: Receiving orders
The sales or account manager for your ecommerce store generates a packing slip based on all orders that match “Paid in full” and “Due to ship.” The packing slip will then be sent to your warehouse manager or a third-party order fulfillment company.
Integrating your ecommerce sales channels with your warehouse systems will make this process more efficient. This way, anytime a customer places an order, a packing slip is automatically generated at your fulfillment warehouse.
Step 2: Picking orders
This is one of the most crucial steps in the pick, pack, and ship process. The right items need to be selected by the picker, and you need an efficient inventory storage strategy to ensure that the warehouse worker knows where to find the right items at all times.
Use a unique tracking number (SKU) for each item. Flyers, catalogs, shipping labels, and other items that are usually sent along with an order should also be made easily accessible.
Step 3: Packing orders
The items picked are then taken to the packing station for packaging. You can save money with packing if you use standard-sized boxes and lightweight packing materials.
You can cut down on your shipping costs significantly by reducing the size of your packaging and using the exact box size you need.
Step 4: Shipping orders
This is the final step. Packaged orders are placed on the loading dock to be picked up by designated carriers. If you use multiple shippers, it's best to have a separate pick-up bay for each carrier.
Types of order picking strategies
It's important to understand the different types of order picking strategies when trying to establish an efficient order fulfillment process. The four most popular strategies used by retailers for picking goods are:
1. Batch picking
This method involves picking orders in batches. Orders are picked only at designated times each day. Large volume fulfillment centers use this method because it is more efficient than picking customer orders anytime a packing slip is generated. Order fulfillment software can help you track and batch orders to avoid errors and speed up the picking process.
2. Zone picking
This method involves dividing a fulfillment warehouse into zones and assigning pickers to each zone. Items are picked from relevant zones and passed to another zone if the order requires items from multiple zones.
This method requires complex coordination, but it is a good technique for large fulfillment centers that handle a wide variety of products. Warehouse management software is vital to making zone picking work seamlessly.
3. Wave picking
This method is a combination of batch picking and zone picking. Pickers will still pick items from assigned zones but will do so for a batch of orders at a designated time each day, instead of picking for every single order.
4. Piece picking
This is the simplest method and it essentially means the picker handpicks each item listed on the packing slip. This method requires the picker to go around the warehouse looking for each item until every item on order has been picked. The method is time-consuming and is suitable only for small businesses that handle just a few orders a day.
Types of inventory management strategies
It is clear that the pick, pack, and ship process will only work if you organize your inventory in a way that guarantees speedy and efficient order management.
In the early days, when you have just a few customers, orders are usually easy to identify and ship. You will have the luxury of time to gather the items for each order and pack them one at a time.
However, as your business grows, you will need a completely different approach. Below are some inventory storage strategies you can adopt for your ecommerce store:
1. Chaotic inventory management
In this method, products are placed randomly on shelves throughout the warehouse. However, products that are related to each other will be placed together. For example, a shelf can hold shoes and clothes, but only shoes and clothes of a particular size and color will be placed on that shelf.
This method reduces errors because it helps workers avoid making mistakes in product categories during picking.
A warehouse management system is essential to making this method work. The software will provide a real-time map of the warehouse to locate where each item is placed and direct pickers to the right shelves. The software will also show your staff the most efficient route to a shelf.
2. Volume-based inventory management
In this method, you will place products with the highest volume of demand closest to the packing station, and products that have much lower customer demand will be stored in the farthest location. This method will save time because pickers will only have to take a few steps before getting to the item they need to pick.
3. Class-based inventory management
Here, you will group items in your warehouse into classes based on shared characteristics. For example, bulky products that require bigger boxes can be grouped together, while fragile items that require special packaging will be placed in a different group.
Should you outsource your order fulfillment?
There are companies that handle warehouse management and order fulfillment for retailers. They will receive the manufactured products from your factory and keep them in storage. When a packing slip is generated for customer orders, the company will pick the products, pack them, and hand them over to your carrier for delivery.
Some popular companies that offer fulfillment services are ShipBob, Red Stag Fulfillment, FedEx, Rakuten, Fulfyld, and Amazon FBA. For ecommerce businesses that lack the infrastructure, experience, and resources to build an in-house fulfillment center, these companies can be a cost-effective solution.
Using a third-party order fulfillment warehouse will give you access to the provider’s expertise in warehousing, fulfillment, and inventory management technology. You will also be able to keep up with the ever-growing demands of customers for faster shipping.
How to pick-pack-ship ultra-efficiently
Customer demands are always evolving and businesses need the right order fulfillment strategies in place to keep up with them. To make your fulfillment process air-tight, scan each barcode twice to ensure that the right products are picked for each order.
Use adequate infill to protect items during shipping, and use the smallest-possible box size to minimize shipping costs. You can take your pack process to the next level using eco-friendly packing materials from noissue. We can even help you design your own branded tissue paper and have it shipped to you in a few weeks.
Remember to assign different loading docks to each carrier to avoid confusion and errors. You should also leverage inventory management software to improve the efficiency of your operations. Follow the tips mentioned above and use the pick-pack-ship method to deliver customer orders in the quickest and most efficient way possible.